Tooling and Engineering Support for Manufacturability
With over 40 years of experience in the aluminum die casting industry, our engineers can ensure improved die life and consistent part production. Explore how we can help you get the most out of your tooling investment.
Kurt Die Casting offers both domestic and import tooling options to meet customer needs and budgets.
How to Enhance Tooling Performance and life in Die Casting
Improved Die Design
- Avoid sharp corners to reduce stress points and heat buildup, preventing cracking.
- Optimize gate location to ensure uniform and rapid metal flow, minimizing tool wear. Utilize advanced software to refine this before production begins.
Select the Right Die Material
- Choose materials that withstand high pressures and temperatures for durability and longevity.
Effective Heat Management
- Implement strategies to manage heat efficiently for improved casting quality and tool lifespan.
Innovative Coatings
- Utilize advanced coatings that protect against wear and tear, reducing maintenance needs.
Efficient Operations and Maintenance
- Regularly inspect and maintain your die casting equipment to ensure peak performance and reduce downtime.
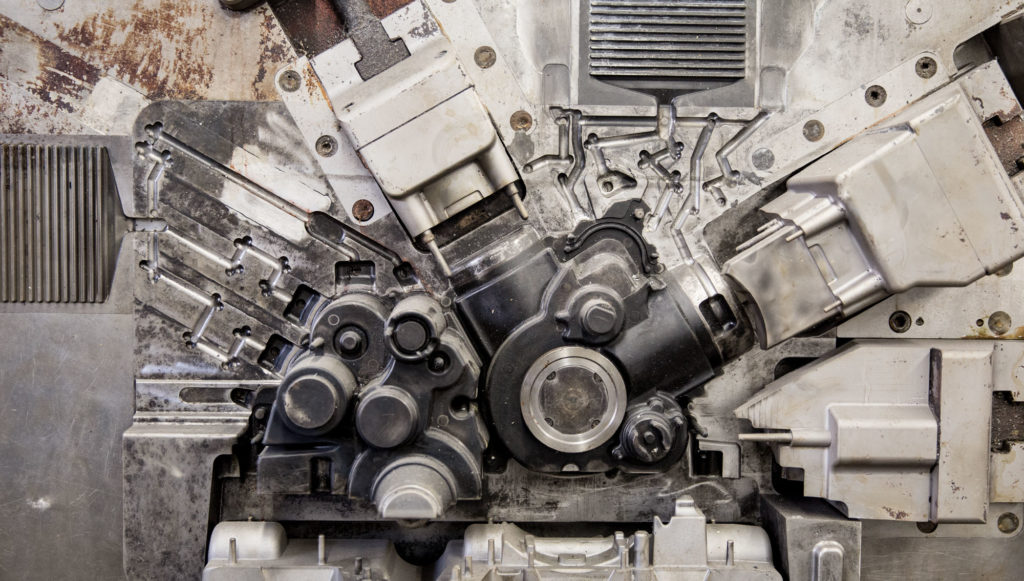
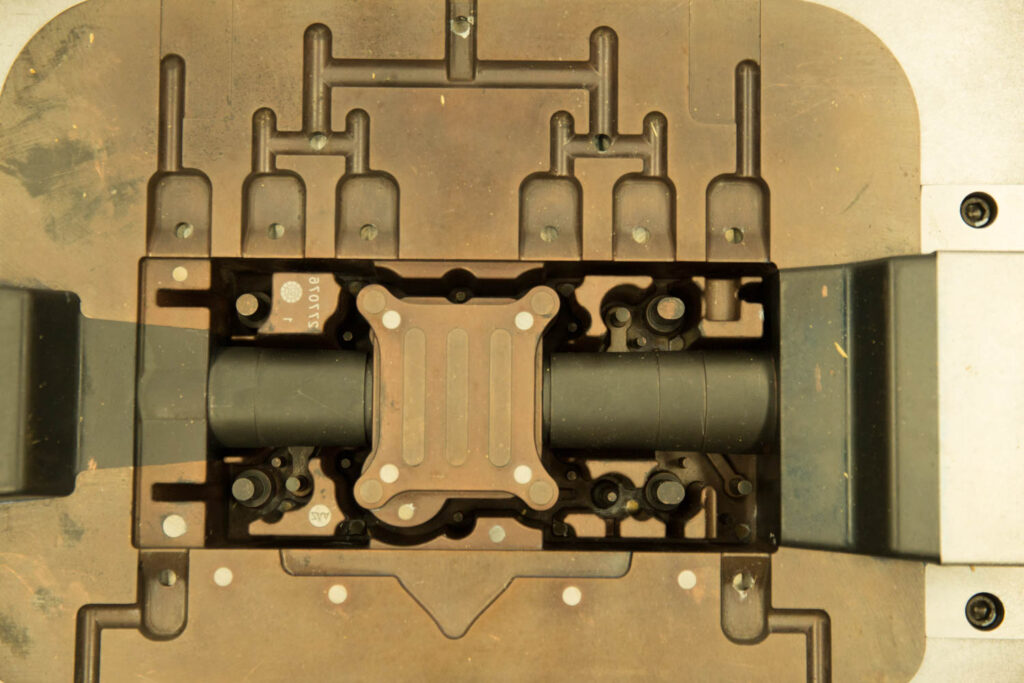
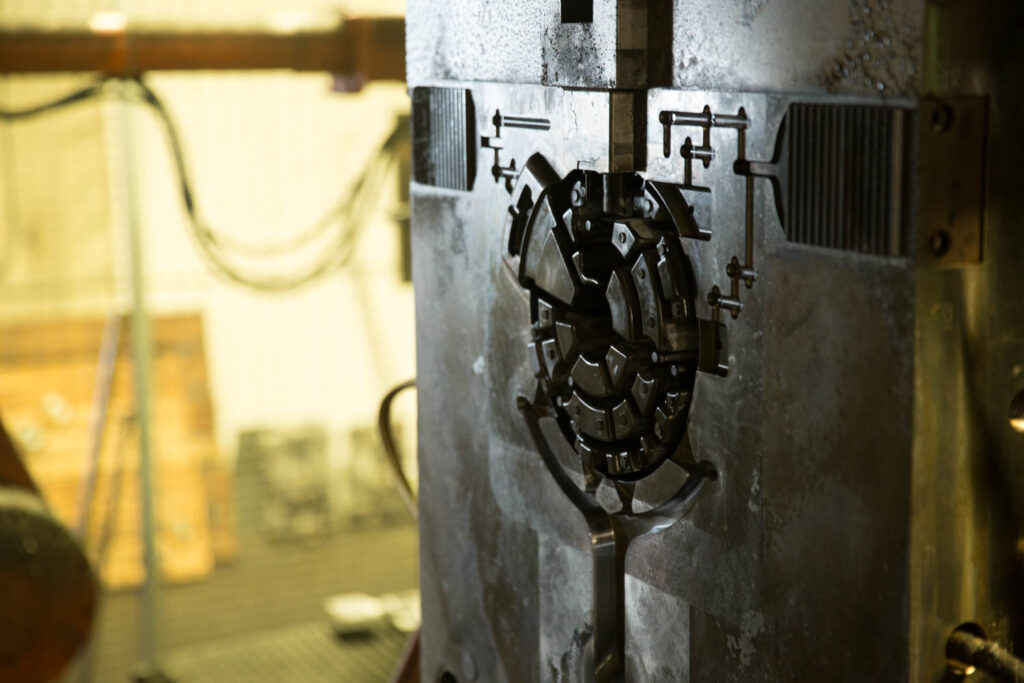
Frequently Asked Questions
What are the key benefits of improving tooling performance?
Enhanced tooling performance leads to longer die life, more consistent parts, reduced maintenance costs, and higher overall efficiency.
How can I ensure uniform metal flow in my die casting process?
Optimizing gate design and using simulation software can help achieve uniform metal flow, reducing wear on your tools.
What role do coatings play in die casting?
Coatings protect die surfaces from wear and corrosion, extending tool life and improving part quality.
How often should die casting equipment be maintained?
Regular maintenance should be performed based on usage frequency and observed wear, typically every few months or as recommended by your equipment provider.